Tootmise digitaliseerimine Saku Metallis: targad lahendused ja pidev töö
Lifti-, rongi-, elektroonika- ja kaitsetööstusele õhukesest lehtmetallist tooteid valmistava Saku Metall Allhanke Tehas ASi juht Rain Johanson selgitab intervjuus, kui kaugele on tehases jõutud tootmise digitaliseerimisega ja mida tähendab pretensioonikas eesmärk Tööstus 4.0.
Saku Metall Allahanke Tehas alustas tarkvaraarendamisega juba kolm-neli aastat tagasi. Ettevõtte juhi Rain Johansoni sõnul oli siis olukord mõnevõrra teistsugune ja vajalikku tarkvara polnud saadaval. Ettevõte kaasas partnerid ja hakkas iseseisvalt lahenduse poole liikuma.
“Tänaseks oleme automaatlao saanud tööle majandustarkvaraga, kus automaatliiniga ühendatud tootmispingid annavad tagasisidet majandustarkvarasse. Lehe kulu kantakse pärast stantsimist automaatselt tootmistellimusele. See tähendab, et kulu osas oleme säästnud ühe andmesisestaja, kes enne sisestas arvutisse infot, mis nüüd toimub automaatselt,” ütles Johanson Tööstusele.
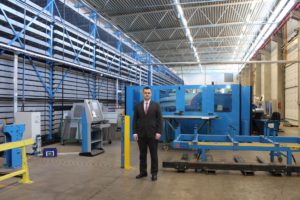
Kuidas süsteemi käivitamine käis, ostsite suure automaatlao 2015. aastal, enne seda pidi ju toimuma ettevõttes põhimõtteline suur otsus, et olemasolevad süsteemid teile ei sobi ning tuleb minna oma süsteemi arendamise teed?
Tootmise infojuhtimise süsteem sai tegelikult enne automaatlao ostmist ära otsustatud. Tol hetkel olime probleemi ees, kus tootmine oli kasvanud piisavalt suureks ning vajadus tekkis online-jälgitavuse järele, infot ei olnud enam võimalik vanal, visuaalsel moel hallata. Nagu öeldud, oli tõsiasi aga see, et vajalikul kujul ei olnud sääraseid programme olemas, valikut ei olnud ja tuli hakata ise arendama.
Kuidas probleemi lahendama hakkav meeskond kokku sai, kes sinna kuulusid?
Meie poolt tootmisjuht, IT-juht ja veel paar spetsialisti. Me ei saa programmeerimist lihtsalt sisse osta – IT-firmadel ei ole tootmise kogemust ega arusaama. Kui minna otse IT-firmasse ja küsida programmi, mis haldab ja jälgib, siis tõenäoliselt ei jõuagi tulemuseni. Oma vajadust ja tarkvara funktsionaalsust tuleb osata väga täpselt kirjeldada.
Kui hõlpsasti toimus asja käivitamine, kuidas ettevõtte töötajad sellega kaasa tulid?
Inimeste jaoks tähendas see käitumise muutmist – nüüd pidid nad hakkama arvutitele ütlema, mis ma teen ja kuidas midagi liigub. See pool oli alguses keeruline. Aga eks iga uue projektiga on tegelikult nii, et kui inimesi kaasa ei saa, siis need käime ei lähe.
Segadust oli palju?
Kindlasti, oli ka neid, kes ei tahtnud harjuda. Juurutusperioodil oli tihti olukord, kus tarkvara andmebaasidega elas oma elu ja tegelik elu oma. Töötajad ei usaldanud arvutit ning palju tuli teha selgitustööd, milliste tingimuste ja käitumismustrite korral on informatsioon arvutist alati autentne.
Kas võib öelda, et teil on tootmises kolm osapoolt – majandustarkvara, mis haldab infot, mis tuleb nii tootmis- kui laosüsteemist – ja eesmärk on, et need kolm poolt jookseksid kokku?
Jah, majandustarkavara, tootmine ja automaatladu omavahel tööle saada on üks suurimaid väljakutseid. Tõsiasi on, et väljakutseid on olnud ja on jätkuvalt piisavalt. Süsteemidega ja riistvaraga on tulnud ette, et müügijutt on ilus, aga pärast soetamist ilmnevad puudused, mida on vaja täiendada. Tarkvaralahendustega on ette tulnud, et soovitud funktsionaalsus ei ole piisav.
Mis need parendamist vajavad osad on?
Süües kasvab isu, meil on juba järgmised mõtted, mis aitaksid tootmist optimeerida. Mida meil praegu ei ole, on kadude registreerimise digitaliseerimine, et saaks kiirelt ülevaate kadudest, miks üks või teine protsess võttis eelkalkuleeritust rohkem aega. See on üks suuremaid lähiaja plaane. Lisaks, tagasisidestamise täiendamine. Täna on töökeskustes digitaalsed tootejoonised, aga mõõteraporteid täidetakse ikka käsitsi. Kokkuvõttes liigub meil üks osa infost tootmises ikkagi veel paberil. Kõige suurem eesmärk on täielik paberivaba tootmine. Kõige kaugem plaan on praegu tootmise peenplaneerimise juurutamine – kui ühes töökeskuses midagi juhtub, siis planeeritaks kogu tehas ümber ning kõikide töökeskuste ressurss on suunatud toodangule, mida on võimalik välja saata.
Millal see peaks toimuma?
Hea küsimus. Samm-sammult liigume selles suunas. Kui enda jaoks lahti mõelda, kuidas seda saavutada, selguvad ikka mingid täiendavad nüansid, mida peab lahendama.
Mis on veel väga konkreetsed näited, mis on tootmises teil nende muutuste tagajärjel muutunud digitaalseks?
Digitaalsed protsessikaardid. Töökeskuses on ekraani pealt näha, mis komponente on operatsiooni teostamiseks vaja, mis on nende laoseis ja mis on järgmine operatsioon. Tootmistöötajate enda jaoks on see oluline – paberil info vananeb ju hetkega, kui info on online’is, on töötajatel kohe live’is selge, et kas kõik tööks vajalik on olemas, ülevaade on jooksvalt parem. Samuti soodustab see tagasiside andmist – üks töökeskus hakkas ka teist motiveerima, et töö sujuvalt jätkuks. Järgmine operatsioon ei saa oma tööd alustada, kui eelmine pole oma operatsiooni lõpetanud. Kvaliteedikontroll oli ka enne kaootilisem, nüüd on see ka osa protsessist, seda ei saa vahele jätta. Kui näiteks painutamise ja keevitamise vahel on kvaliteedikontrolli operatsioon, siis keevitaja ei saa alustada oma operatsiooniga enne kui eelnev, ka kvaliteedikontroll, on tehtud.
Mainisite tootejooniste digitaliseerimise täiendamist. Kuidas see protsess jätkub?
Praegu tuleb tootejoonise otsimiseks lugeda detaililt tootenumber ning sisestatada see arvutisse käsitsi. Plaan on üle minna QR-koodide kasutamisele. Praegu on koodi sisestamine kõige aeglasem osa jooniste vaatamise protsessis ning QR-kood aitaks seda kiirendada. Kõik toodetavad detailid on vaja selle tarvis varustada kleebistega, kus ühes otsas on tootmistellimuse number ja teises on detaili tähis. Tootmist läbib meil üle 10 000 detaili nädalas ja see arv kasvab pidevalt.
Millised näiteid võiksite tuua, mida saaks veel digitaliseerida?
Värviliin. Praegu toimub automaatvärviliinil juhtimine ikkagi käsitsi – kas pesust läbi või mitte, millised on selle värvi küpsusparameetrid ahjus –, kõik need otsused sisestatakse manuaalselt. Ideaalis oleks nii, et majandustarkvarasse on kirjeldatud värvimisliini marsruut pluss vajalik retsept, kuidas ahjus parameetrid peavad olema. Detaili liinile jõudes registreeritakse QR-koodiga toode ning edasine käsitlus toimub automaatselt.
Kui vaadata turgu üldisemalt, kas sääraste lahenduste pakkujaid, insenere on meil turult võtta või on pakkumine väga väike?
Pakkujaid on palju, aga keeruline on ära tunda, milline neist on õige ja sobilik. Üks oluline aspekt, mida hindame, on järjepidevus, et koostööpartnerid oleksid kolme, viie või kümne aasta pärast ka olemas ja koostöö jätkuks läbi aastate. Partnerite suurust ja usaldusväärsust peab eelnevalt kriitiliselt kaaluma.
Tööstus 4.0 on ilus katusnimi, mis koondab palju tegevusi. Mis see Tööstus 4.0 on, kui automaatne see peaks olema, et saaksime nimetada ühte tootmist nii uhkelt?
Tuleb tunnistada, et kuna me ei räägi suurtest partiidest – meie tootmine on ikka tellimuspõhine –, ei saa me kunagi 100% robotite peale minna. Eks väljakutse ongi, kuidas maksimaalselt digitaliseerida käsioperatsioone.
Kuidas hindate – olete ise kõik viimased kui ideed ritta pannud, mida üldse saaks veel teha digitaliseerimise suunal?
Kindlasti mitte, tänasel päeval on maailmas kindlasti palju lahendusi, mida me ei pruugi praegu teadagi. Siselogistika ei ole meil veel näiteks kuigi heal tasemel. Selles osas on palju kinni inimeste peades, kuni viimaste väikeste asjadeni – kuidas materjalid liiguvad, kus on parkla- ja riiulikohad ja et seda kõike toetaks ka majandustarkvara. Selle aasta sees on plaanis jõuda ka selleni, et meil oleksid ka kindlaks määratud siselogistikud, kellel jookseb ees nimekiri, kus midagi valmis sai ja kuhu ladustatakse, millist detaili on järgmiseks kellelgi vaja mingi töö tegemiseks ja nii edasi.
Kui lüüa kokku kõik digitaliseerimisega seotud väljaminekud – robotliin, tarkvara arendus, töökeskused ja arvutid –, siis kui suur see digitaaliseerimise protsessi koguinvesteering on olnud?
Seda on raske öelda, sest kõik see on olnud normaalne areng, proovime soetada ainult viimast tehnoloogiat või lahendusi. Pelgalt tarkvarale on kulunud paarsada tuhat eurot aastas.
Lauri Leet, kaasautor
Harro Puusild, Tööstusuudised.ee
Tagasi